In the coming months, the PivotBuoy® wind floating platform will be installed in Gran Canaria. The turbine, a Vestas V29 225kW, left Vestas and arrived last month with the adapted drivetrain ready to rotate in a downwind configuration. X1 Wind’s electrical team is currently integrating and testing all the electrical and communications systems to check their readiness to operate, and the adaptation works on the turbine will be soon finished.
X1 Wind adaptation of a Vestas V29 turbine to downwind configuration
August 25, 2020
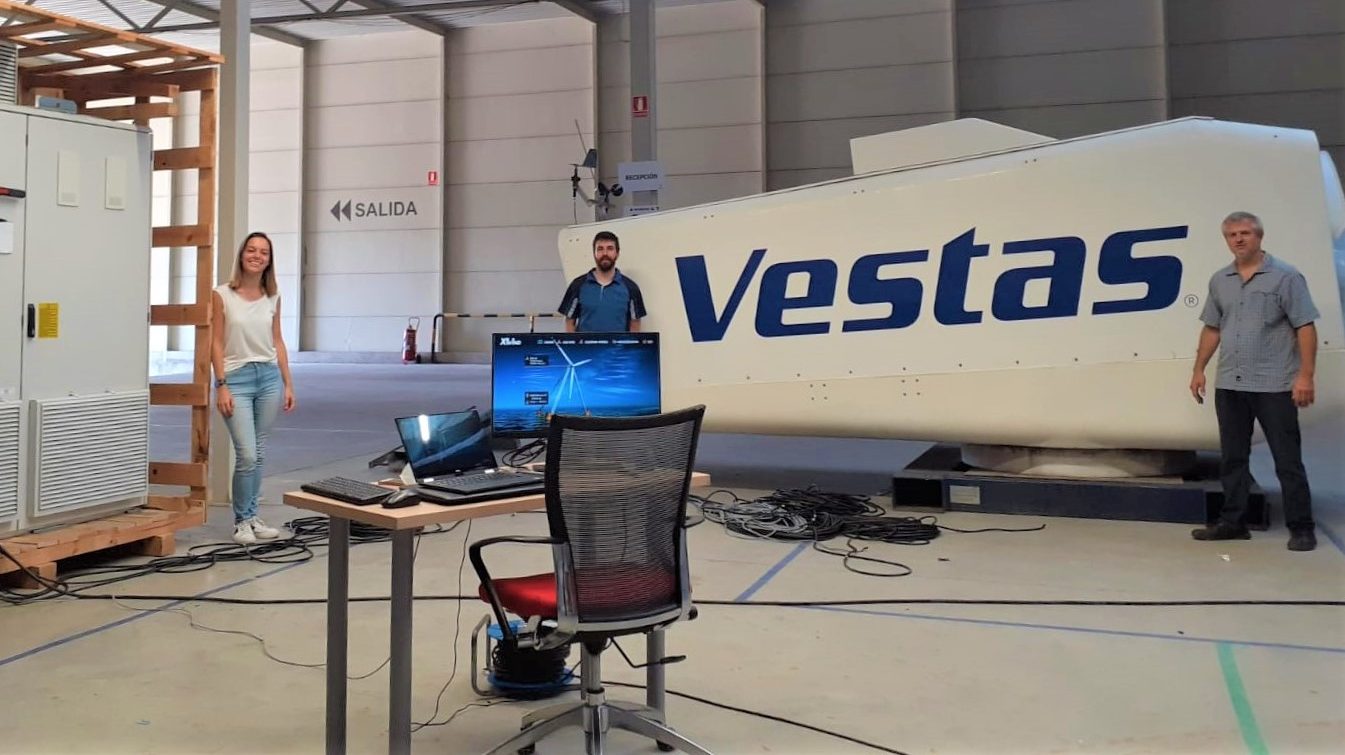
X1 Wind team members with the Vestas V29 nacelle
Wind turbines have historically been mounted in an upwind configuration, with the rotor facing the wind. This is done to minimize the so-called tower shadow effect, which is significant in traditional downwind tower structures. However, over the last decades, turbine blades are getting longer, and with 100 m+ blades, avoiding tower strike becomes a great challenge. That is why significant effort is being put in the development of specific solutions with the goal of increasing the distance between the blades and the tower. Some common strategies include using a tilt angle or rotor coning, which lead to generation inefficiencies. Other widely used solutions with the same purpose include pre-bending of the blades and increased hub overhang. Additionally, specific control strategies and the use of stiffer, heavier blades is required, resulting in considerable increase in the cost of blade manufacturing.
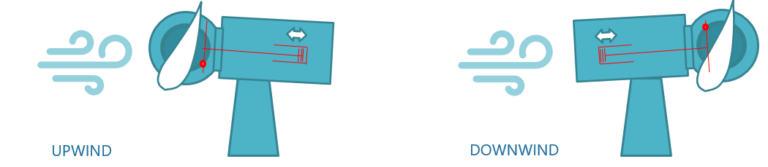
Upwind vs Downwind orientation of wind turbines
What if we could remove this constraint? By switching from upwind to downwind configuration, with the nacelle facing the wind first, we can avoid this constraint altogether, unlocking potential lighter and more flexible designs, key characteristics for the efficient development of truly gigantic wind turbines (ongoing research such as the SUMR project led by the University of Virginia, Sandia National Labs and NREL funded by the Department of Energy in the US are working on the design of extreme-scale downwind blades that are 200 meters long which could power 50-megawatt in the future).
It is known that one of the main drawbacks of downwind is the tower shadow, and one of the main reasons for its seldom use. However, the PivotBuoy® platform has been designed to minimize this effect. By having a floating platform instead of a fixed structure, it is possible to allow the whole structure to weather-vane and orientate passively with the wind. This feature enables a complete redesign of the structure avoiding large towers, which need to cope with the increasing bending moments.
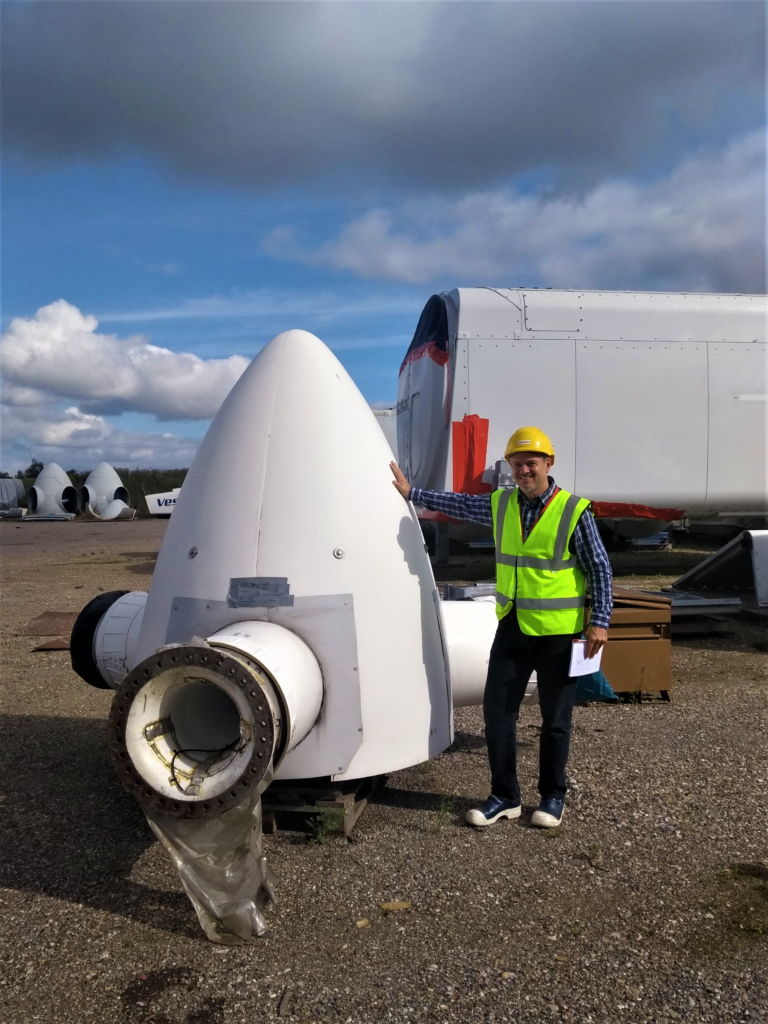
X1 Wind team member Santiago Canedo, responsible for the turbine adaptation, at Vestas facilities
How are we doing it?
X1 Wind aims to show the benefits of this innovative solution that will allow larger and cheaper floating wind turbines using downwind technology by testing a prototype in the Canary Islands. To that end, Santiago Canedo, a mechanical engineer with 18+ years’ experience in wind turbine design including GE’s Haliade X-12MW, is leading the X1Wind mechanical team in the project of converting an upwind Vestas V29 225kW into a downwind configuration, to be tested with the PivotBuoy® platform. The adaptation process has the following stages:
- Adaptation of the drivetrain: since it will counter-rotate, the gears have been machined to be able to work on the opposing flank. This has been done by Kumera, a manufacturer of mechanical power transmissions for the industrial market with more than 70 years of experience.
- Connection of the generator: it will spin in the opposite direction; therefore, the connections must be changed to counter-rotate
- Final minor adjustments to pitch and lubrication systems.
- Re-positioning of the turbine and blades to orientate the rotor in a downwind configuration, as shown in the image:
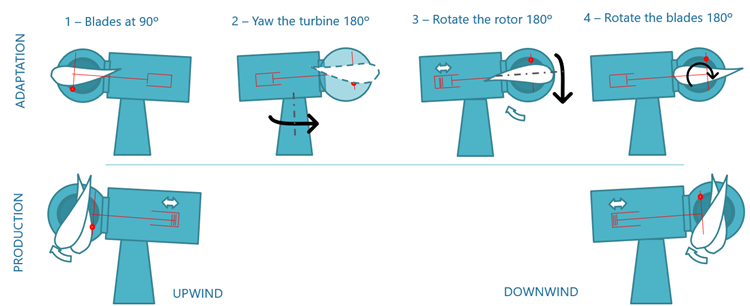
V29 downwind adaptation process
Despite the transformation, the rotor will still be spinning clockwise. The original yaw system will be blocked for operation, since the PivotBuoy® system self-aligns with the wind thanks to its unique weather-vanning ability. This reduces the amount of active systems of the platform, which is critical for Operation and Maintenance during the lifespan of the system.
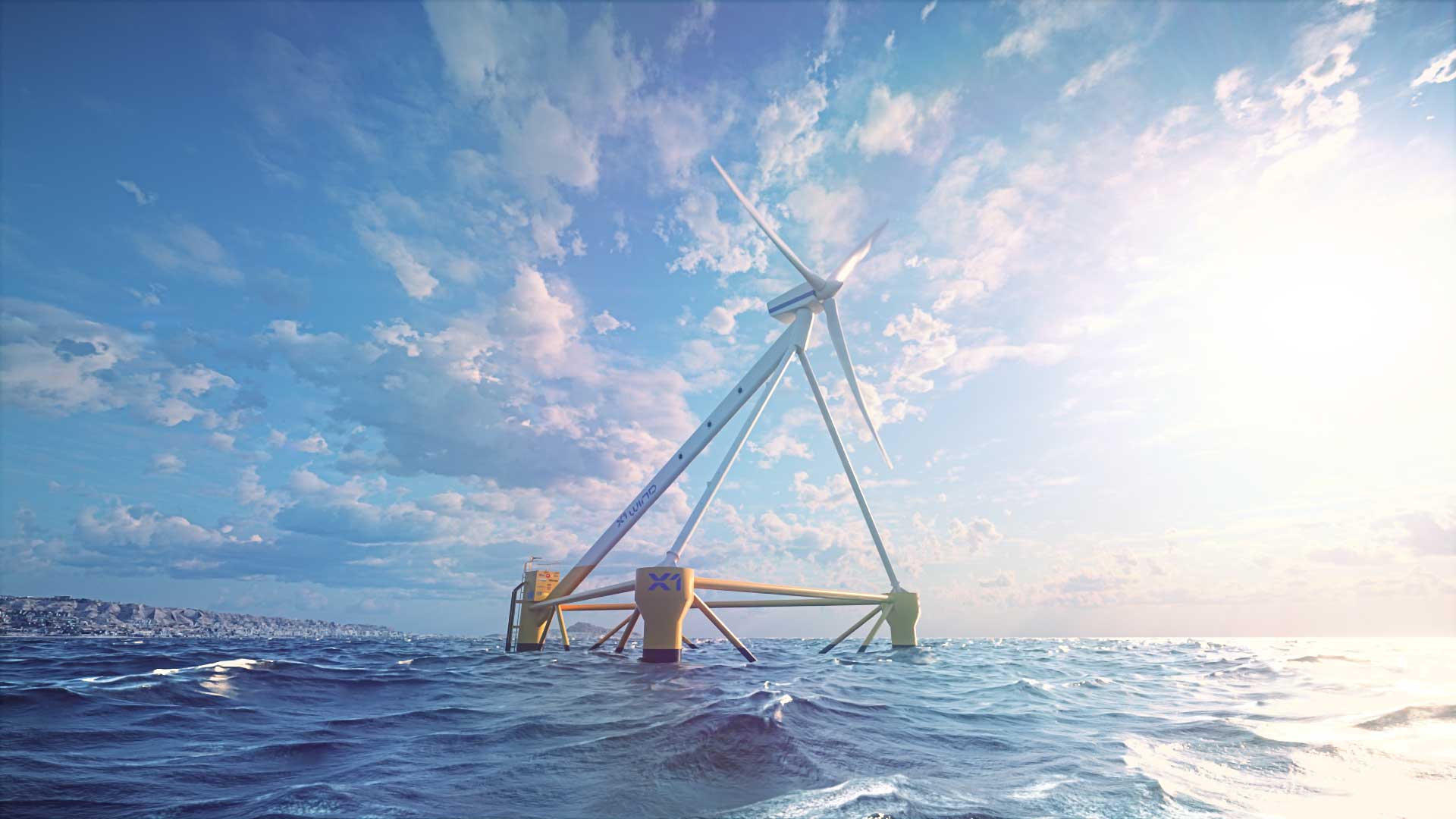
X1 Wind’s V29 turbine in downwind configuration to be installed at PLOCAN test site
About X1Wind
X1 Wind mission is to provide highly scalable solutions to reduce carbon emissions and provide affordable clean energy globally. In the last years, X1 Wind has continued to develop its disruptive floating wind technology, completing the design of a fully functional part-scale demonstrator, and successfully executing several testing campaigns, putting together a team of experts with decades of experience in the offshore wind and marine sectors. The company has been recognized as one of the cleantech start-ups with highest potential impact in Europe.
About CDTI – NEOTEC Program
The adaptation of the turbine to downwind has been partly funded by the Centre for the Development of Industrial Technology (CDTI) through the NEOTEC program to support technology-based startups based in Spain.
The Centre for the Development of Industrial Technology (CDTI) is a Public Business Entity, answering to the Ministry of Economy, Industry and Competitiveness, which fosters the technological development and innovation of Spanish companies. It is the entity that channels the funding and support applications for national and international R&D&i projects of Spanish companies.
About PivotBuoy
The PivotBuoy Project aims to validate the benefits of the PivotBuoy® mooring system, An Advanced System for Cost-effective and Reliable Mooring, Connection, Installation & Operation of Floating Wind. While the scope of the project is on demonstrating the innovative PivotBuoy® single point mooring system, it will also enable the test of the Vestas V29 turbine adapted in a downwind configuration in real floating conditions at PLOCAN test site in the Canary Islands.
The Consortium is formed by nine partners from five different countries: X1Wind, ESM, WavEC, PLOCAN, INTECSEA, EDP, DTU, DNV GL and DEGIMA. The project officially started in April 2019 and will last for 36 months.
About Innoenergy
X1Wind is backed by InnoEnergy, the biggest European company promoting innovation and entrepreneurship in sustainable energy. InnoEnergy supports and invests in innovation at every stage of the journey – from classroom to customers. With their network of partners they build connections across Europe, bringing together inventors and industry, entrepreneurs and markets, graduates and employers, researchers and businesses. They work in three essential areas on the innovation mix: education, product innovation and business creation.
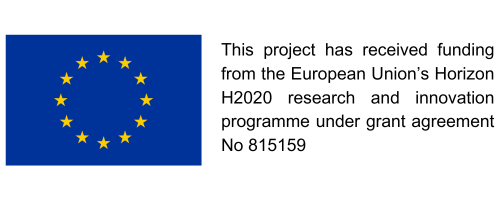